Leyland P76 Owners 2005 |
Technical Information |
|
Clutch plate 3 0r 6 bolts
by Jason
- As a mechanic, owning a mechanical workshop, you get to see lots of strange things with cars. Earlier this year I had a fellow club members P76 V8 4 speed in to do some steering work & get it ready for rego (amongst other things) & immediately noticed that there was a terrible vibration in the engine.
- Now, it was awful!!!. At low revs (1500rpm) a low speed vibration went through the whole car, to
- the extent that if you had the door open, it would shake up & down in time with the vibration.
- The exterior sun visor would also do a "jiggle" as well! When you brought the revs up to 4000rpm the whole dash shuddered & the car was most unhappy.
- The first priority was to make the car safe & driveable & of course, getting the all important registration "pink slip", so the vibration was put in the "too hard basket".
- I had suspected something was wrong in the clutch/flywheel area, cause if you rested your foot on the clutch pedal whilst you were feeling these vibrations, the clutch pedal did a little dance in time with the vibration.
- The clutch also shuddered on take off, which is not all that unusual for the P76.
- Anyway, fast forward to now, & the Leyland has forced the issue, with the owner reporting a "filthy" noise from the bell housing area & the clutch now not dis-engaging properly, making gear
- shifting difficult.
- By the time the big rig got to me, the noise had gone, but the clutch woes remained. The "take up point" of the clutch was now right on the floor, so it was time to slip the gearbox out & have a poke around inside.
- Getting the box out of the Leyland is too easy, compared with modern cars.
- The rocker cover gaskets & engine rear seal have been seriously leaking.
- There was enough oil underneath the car to make the "Exxon Valdez" oil spill look like WD40 over spray!! With the box out & bell housing off, it all became clear. One of the pressure plate securing bolts had decided it was time for a holiday & parted company. The noise thatthe owner had heard was the bolt rattling around inside the bell housing.
- It had at one stage gotten jammed between the flywheel & the bottom of the bell housing, cracking the bottom of the alloy housing, before exiting via the clutch fork hole. The other two bolts holding the pressure plate to the flywheel (The P76, along with Holden's, Fords & Valliant's of that era only had 3 securing bolts) were also loose.
- The pressure plate was able to move around on the flywheel & the missing bolt had allowed the pressure platediaphragm to distort, it was all pretty ugly.
- My main concern was still with this engine vibration & I was hoping that the pressure plate "flopping around" was the answer.
- I took off the pressure plate & ran the engine with just the flywheel & it was much better, not perfect, but definitely improved, you probably wouldn't pick it if you weren't looking for it.
- I couldn't try it with the pressure plate on at that stage, as the thread in the flywheel for the offending bolt was stripped.
- I went to a trade night a while back, put on by the local clutch mob & Daiken clutch industries, & I remember Daiken, (who are an original equipment clutch supplier to many Japanese vehicles) giving PBR (who are an Australian Original equipment clutch supplier), a good ribbing about these "3 bolt" pressure plates.
- Their argument was that with a clutch of that diameter, 3 bolts are not adequate to provide even clamping of the pressure plate to the flywheel, resulting in distortion of the diaphragm (the big steel spring that clamps the whole "she-bang" together) & resulting in clutch shudder.
- Now seeing that there isn't a Jap car with a 3 bolt pressure plate & that on a whole, their clutches work beautifully, I reckon there might be some truth in what they say.
- Now, put that all on hold & we go to MY P76, & the fact that I will be changing my car to a 5-speed manual, but more about that in another issue.
- One of the things that I have had done was to convert the new clutch & flywheel that I will be using on my car to a 6 bolt pressure plate.
- I sent the new 3-bolt pressure plate & the machined & lightened V8 flywheel away to have the other three holes drilled in the flywheel in the correct spots, so that all the threaded holes are of equal distance apart.
- So I then bolted my 6-bolt pressure plate to his 3-bolt pressure plate, so as to provide a
- template to drill the holes in his pressure plate. After drilling the holes I then bolted it to his flywheel to provide a template to drill & tap the holes in the flywheel, phewww!! Lots of templates, lots of holes & lots of flywheels huh! But anyway, to make a long story shorter (not short, it's passed that now!) we now have a 6- bolt flywheel & pressure plate for the vibrating Leyland.
- Now I can hear the technical ones amongst you saying "why didn't you do all this to a new clutch?" well, the poor suffering club member had a new clutch fitted 18 months earlier & only done 10,000 odd kays since, so there was negligible wear on the unit.
- The only sus point about the assembly was the possible distortion of the pressure plate caused by the missing/loose bolts.
- When removing the pressure plate from the flywheel, you should always loosen the bolts evenly to avoid distorting (bending) of the pressure plate & when all this fell apart in the bell housing, that didn't happen, still I reckon it is worth the risk of using the old pressure plate to try & keep the costs down, as I am going to get rid of all that awful clutch linkage & use a commodore clutch cabled to get a "lighter, smoother" clutch pedal.
- Anyway, I banged the "modified" clutch assembly/flywheel back on to the engine & fired it up to check for the vibration, with mixed results.
- I don't know whether it's because I am trying to feel for a problem, but I still wasn't 100% happy with it.
- Leyland engines, when manufactured, were "dynamically balanced", which means they were spun up & balanced with different weight bolts that screw into the flywheel/flex plate at points around the circumference of the flywheel.
- The harmonic balancer at the front of the engine (front pulley) was also balanced. What I did next will probably raise a few eyebrows, but I tried the balancing bolt on the flywheel in a few different positions & in the end, achieved a pretty damn good result.
- So there we have it.
- A smooth engine & 6 bolt clutch. The next rave will be about the cable clutch modification, which Russell Nicholson's has done on his V8 5speed with really excellent results.
Wed, 8 Dec 2004 From: "Mike Chadwick"
Subject: RE: [leylandp76] leyland legends 6
- Jason,
- I shudder in writing to a mechanic, because I know you know your business better than I do.
- That vibration certainly gave you the run-around.
- The 'floating' clutch and lose bolt were obviously the main causes, and gave you an adventure and us a good story. But did you check for inlet manifold leaks?
- I only asked because you didn't mention it, and I have occasionally discovered that to be a cause of vibration.
- I have also known a cured inlet manifold leak to relieve clutch judder on take-off.
- From what you write, "I took off the pressure plate & ran the engine with just the flywheel & it was much better, not perfect, but definitely improved, you probably wouldn't pick it if you weren't looking for it.", with only the flywheel in situ, there was still some vibration.
- It's the "not perfect" bit that I'm pursuing.
- Perhaps I'm too fussy; if so please forgive me.
- I used to own a V8 flywheel with 3 pairs of holes (6 altogether, but not evenly spaced) which I presumed (but I'm not certain) to be a Terrier flywheel.
- I always had to drill the extra holes in the new pressure plate whenever I changed the clutch.
- The improvement in operation was only good as long as the clevis pins in the pedal and linkages were in good condition.
- To overcome that I fitted needle roller bearings with a 5/16" ID in every place where a clevis pin is fitted in the standard clutch lifting mechanism, and that relieved the contrary rotating pull on the clevis pins every time the clutch is used.
- The feel was light and the clutch was always predictable, and never developed that heaviness again.
- For the purist, you can't tell the difference from standard until dismantled.
- However, the support bracket on the driver's side frame member still needs to be reinforced.
- Mike Chadwick.
|
|
|
|
Last updated Feb, 2010 |
This web site may contain Copyright material
If you find any problems with the site, please email the
Web Editor 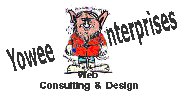 |
|